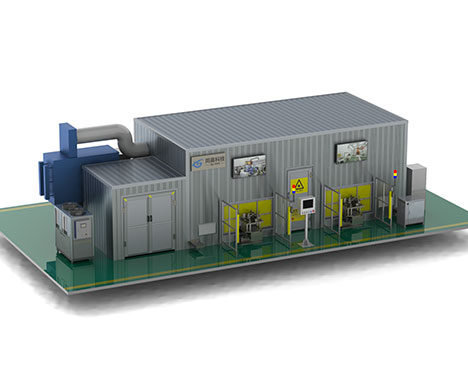
- Project Overview
- Project proposals
- Project Craft
- Project equipment list
- Project site photos
Kehua Holdings Co., Ltd. specializes in the production of automotive turbocharger parts and is one of the most competitive suppliers in the international market of automotive turbocharger parts. Its products are exported to North America, South America, Europe, Japan, South Korea, etc. area.
The turbocharger system can effectively improve the engine power performance and fuel efficiency. Due to the turbocharger working at high temperature, the shape of the shell is complex, the dimensional accuracy and surface quality are extremely high, especially the welding of dissimilar materials in its components , Is always the bottleneck of its product process optimization.
Recently, for the welding process of the turbine shifter, we have independently developed and integrated a set of fully automatic turbine shifter laser welding station with Hi-Tech and Kehua Co., Ltd., which can be applied to 8 kinds of turbine products, and the annual output is up to 1 million sets.
The crank material in the turbocharger lever is 316 ti JIS, and the material of the rocker arm is 1.4848 EN. The material parameters of the two are very different. Welding cracks are easily formed during welding and tend to be hardened. Therefore, when using the traditional non-melting electrode gas shielded welding (TIG) process, it encountered a series of problems such as shallow penetration, low deposition speed, low welding strength, and low production efficiency.
圖1:TIG工藝與激光工藝優(yōu)缺點(diǎn)對比圖
The laser welding process independently developed by Hi-Tech makes full use of the characteristics of laser coherence, which solves the problems of partial fusion and non-fusion of welds, and at the same time ensures the consistency of the entire weld, especially automatic welding. The application of quality online system guarantees the satisfaction of the final quality of all products.
圖2:渦輪增壓器焊接質(zhì)量對比圖
In addition, laser welding significantly reduces the process cycle time. It takes only 1-2 seconds to weld a turbine lever, which is more than tens of times higher than traditional TIG, although the cost of laser equipment is much higher than that of TIG system. However, under this efficient operation, the unit price of the actual product has been significantly reduced, and at the same time, the technological competitiveness of the product has also been improved.
圖3:渦輪撥桿激光焊接站
The workstation integrates a large number of high-tech, including high-precision automatic inspection system, high-precision automatic feeding system, high-precision welding seam tracking system, high-power laser welding system and high-precision remote galvanometer system, which is a fully automated high-speed and stable volume Provide strong support!
圖4:正在進(jìn)行焊接作業(yè)的機(jī)器人
Products are attached to the market, and good products can greatly improve the core competitiveness of enterprises. In the future, Tong Hi-Tech will strengthen independent innovation, effectively upgrade the technical grade and added value of its main products, broaden new channels and open up new markets, actively carry out cooperation with general industrial industries, and continue to in-depth research and development and promote products and products that meet market needs. The plan is to create a lean, efficient and environmentally friendly high-tech industry benchmarking enterprise that conforms to the general direction of "Made in China 2025".
Next:None